WITH A FAST SOLUTION AND IMPROVEMENTS, DHL SUPPLY CHAIN STREAMLINES THE LOGISTICS OF SPARE PARTS FOR AGCO'S AGRICULTURAL EQUIPMENT
Press Release: São Paulo, December 2, 2020
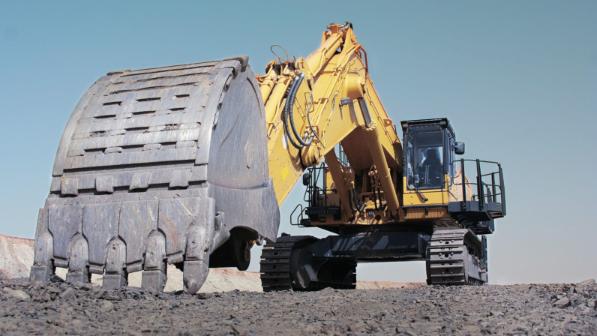
- DHL Supply Chain is responsible for the storage and shipping of parts for agricultural equipment of the brands Valtra, Massey Ferguson, GSI, Challenger, Fendt, and PrecisionPlant
- With 110 thousand SKUs and almost 1 million pieces transported per month, the operation stands out due to its complexity level and scope
As an essential service, the agricultural market cannot stop and one of the key inputs is the spare parts for equipment. To support this flow, DHL Supply Chain, the global leader in contract logistics, has developed a fast solution that, along with other improvements, has streamlined and made more efficient the delivery logistics of spare parts AGCO Parts, an AGCO company - the world leader in design, manufacturing and distribution of agricultural solutions. Now, shipments for urgent orders are carried out in up to two hours (enabling deliveries in up to 24 hours) and improvements in terms of processes and systems have increased the stock accuracy index to 99.85%, which reduces errors and delays.
DHL Supply Chain has managed AGCO's Distribution Center located in Jundiaí (SP) since 2018, being responsible for the storage, shipping and packaging areas. The Distribution Center has approximately 34 thousand m² of total area, where about 1 million items are carefully handled every month. AGCO Parts' equipment parts for tractors, harvesters, sprayers, seeders and planters are shipped to more than 590 distributors and dealers of AGCO's brand throughout Brazil and some countries in Latin America.
For Adriano Medeiros, Director of Operations at DHL Supply Chain, “the agricultural market is one of the most resilient to the pandemic, maintaining - and in some cases even expanding - its production and export levels. In this sense, receiving spare parts quickly and with high assertiveness avoids losses in the harvest and provides an important differential for our customer in terms of service provision and quality of service.”
“We seek the help of DHL Supply Chain to assist us in improving our operational efficiency. This partnership brought us innovative solutions in our areas of inbound, picking, storage, outbound, among others, due to the vast experience and knowledge of DHL Supply Chain regarding the entire logistics operation. We are very pleased with the results obtained and these actions gave us the opportunity to offer an innovative experience to our customers,” says Marcelo Traldi, Vice President of Aftermarket Services for South America at AGCO.
The director at DHL Supply Chain points out that “this operation stands out for the volume and variety of the parts that are handled. There are about 110 thousand SKUs and 60 thousand lines shipped / month, with dimensions ranging from 1 gram to 750 kg and from 1 mm to 15 meters, which makes the operation quite complex. However, through our experience and team of experts, with next generation processes and software and proven management methodology, it was possible to design a more efficient and robust solution that have brought many gains to the client. The reliability of the solution and the operational capacity of DHL Supply Chain were also decisive factors for the success of the partnership.”
DHL Supply Chain's work begins with the receipt process and continues with the conference, then the quality check and, finally, the packaging of products. After the parts are stored they go through inventory management, slotting, kits assembly, picking, and parts checkout. It is important to note that the warehouse has 15 types of locations, in more than 170 thousand different addresses. The management of all this stock is made by an experienced inventory team that, assisted by the functionalities of the Warehouse Management System (WMS), has been working hard to ensure record stock accuracy in the operation.
“Through the warehouse management system, we are able to track the performance of our team on an hourly basis and we also have a full visibility of our operations. Our coordinators track the numbers through their tablets and provide online feedback to every team member. Thus, we also gain more agility and efficiency to ensure the delivery of parts to customers within the contracted terms - a fundamental aspect to consider in the aftermarket segment,” says Adriano Medeiros.
Further innovations used on the Distribution Center are the Cubescan (equipment used to measure the cubage and weight of items on the moment of receipt) and the Ring Scanner (a kind of computerized watch that leaves the hands of the operator free and facilitates the process of picking and parts checking in the warehouse), which ensure greater productivity in the execution of activities and, consequently, more competitive costs.