No industry has escaped the impact of the coronavirus crisis, but each sector has faced its own unique set of problems. For engineering and manufacturing companies, the first waves of the pandemic forced a rapid reconfiguration of operations on the ground. Factory staff can’t work from home, so companies had to make their facilities safe for employees. They have modified their processes, adapted shopfloor layouts and introduced new protective measures, all with remarkable speed.
Through conversations with dozens of leading players across the sector, Gantier and his team have identified half a dozen big opportunities for engineering, manufacturing and energy sector companies to achieve significant improvements to their supply chains and logistics processes.
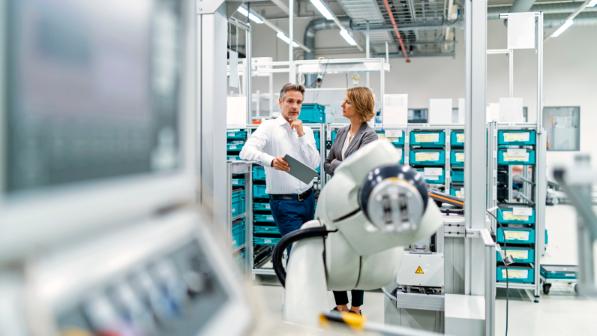
1. Accelerate your digital transformation
The crisis forced everybody to embrace digital tools, as video calls replaced face-to-face meetings and people shifted to remote working models where the roles allowed. But most companies also had ambitious digital plans before the coronavirus, recognizing the power of automation and seamless information flows to streamline processes and improve efficiency.
Supply chains are ideal candidates for digitalization. Technology can give companies the visibility they need to improve planning, monitor execution and keep customers informed. Nevertheless, the complex nature of supply chains, with multiple participants and moving parts spread around the world, makes it harder to build those digital links. With limited resources and other challenges to tackle, companies might be tempted to delay their supply chain digitalization projects.
They should resist that temptation, says Gantier. “Digitalization is a key enabler for the new generation of fast, flexible and cost-effective supply chains. Accurate, timely information helps companies to optimize their existing supply chain operations, and the insights derived from good data unlock most of the improvement opportunities we have identified for our customers.”
2. Know and manage your supplier footprint
Supply disruptions related to the pandemic have made companies think harder about supply chain risk. Sourcing critical components from a single supplier, or sourcing multiple components from suppliers concentrated in a single region, can leave companies with no room for maneuver when problems occur.
To manage and mitigate such risks, companies first need to understand them. That requires systematic analysis of an organization’s supply base in order to understand its risk exposure and the potential impact of disruptive events. And because supply chain problems can emerge very rapidly, companies need robust monitoring/early-warning systems too. Smart digital risk management tools, including DHL’s own Resilience 360 platform (recently rebranded as Everstream Analytics), can help out, says Gantier, by tracking events in near real time and alerting companies to incidents that could affect their supply chain operations.
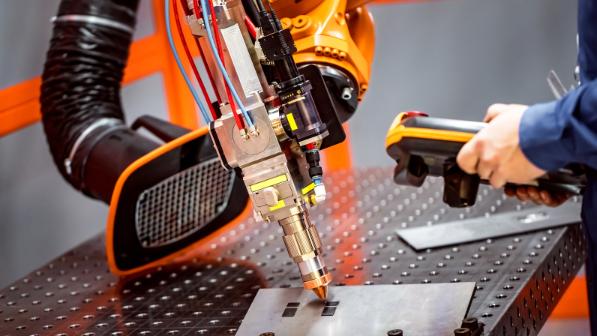
One of the best ways to reduce the risks associated with concentrated supplier footprints is to diversify. Sourcing critical components from multiple suppliers in different regions significantly lessens the impact of any single disruptive event. This trend was already underway before the crisis, notes Gantier, with a third of companies looking to diversify their supply base as a hedge against rising tariffs and trade tensions. The post-pandemic quest for resilient supply chains is only likely to accelerate such moves.
3. Build flexible warehouse networks
The storage and distribution of finished goods, spares and service parts is a significant challenge for many engineering-based businesses. Portfolios of complex products create the need for extensive inventories, while customers demand high levels of availability and responsiveness to keep business-critical equipment working. The best way to keep service levels up and transport costs down is to store parts close to the end user, but that can lead to extensive networks of costly – and often inefficient – warehouses.
“An engineering or manufacturing player doesn’t want to own lots of warehouses,” says Gantier, “They’re expensive assets, and it’s always difficult to ensure you have the right capacity in the right place to best serve your customers.” Increasingly, he says, companies are pursuing a more flexible option: leasing warehouse capacity from an external provider, which can also provide the skills and resources necessary for efficient operation.
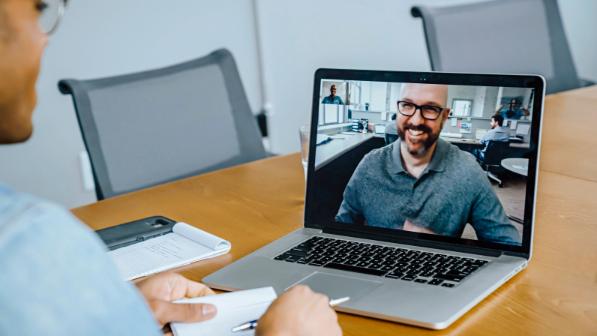
Since the start of the pandemic, he adds, DHL has gone one step further and bought warehouse facilities from customers and incorporated them into its own network.
4. Optimize your inventory
Why go looking for the latest logistics stories and insights when you can have them delivered right to you?
5. Get your supply chain management costs under control
With resources depleted after a year of lockdowns and slowdowns, cost and cash management are going to be top priorities for companies in the coming months. Under pressure to reduce costs wherever they can, supply chain and logistics functions will be looking for tactical opportunities to make savings on everyday expenditures such as packaging and freight costs.
The challenge for many organizations, says Gantier, is balancing savings benefits against the work required to find and secure the best prices. “Buying freight on the spot market can be a very efficient way to access the best cost option for a one-off or low-frequency shipment,” he says. “But each purchase from a new supplier creates additional work downstream to manage invoices, arrange payment and audit the whole transaction to ensure the agreed terms have been met.”
This, however, is another area where new digital tools are helping to streamline the process. The development of blockchain-based, digital freight marketplaces, for example, now allows companies to make one-off transactions in a secure, traceable environment, with all the relevant documentation and transaction data generated automatically at the click of a button.
An even more powerful way to simplify logistics purchasing is to outsource the whole process to specialists. The use of lead logistics partner (LLP) arrangements, in which a third-party organization takes over the management of the end-to-end logistics process, has been increasing in many sectors over recent years. Gantier notes that a growing number of engineering and manufacturing players are adopting the approach as they review their post-pandemic supply chain strategies.
6. Embrace the power of e-commerce
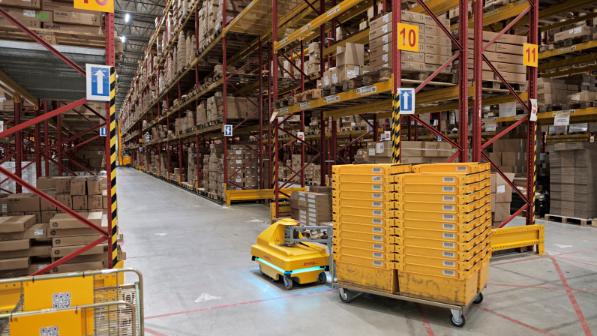
From recovery to sustainable growth
Improvements to supply chains and logistics processes will help companies meet their immediate-term operational and commercial challenges, but they also have an important longer-term role, says Gantier. “We will be dealing with the fallout from the COVID-19 crisis for some time to come, but engineering companies are also preparing for other big changes, especially climate change and the transition to a net-zero economy. Supply chain capabilities honed during this crisis will also help organizations to address those challenges.” — Jonathan Ward
Published: March 2021
Images: Maciej Bledowski/Alamy/mauritius images; Adobe Stock; Daniel Ingold/Westend61/ullstein; ddp; BO/Blend Images/ddp; Adobe Stock; DHL