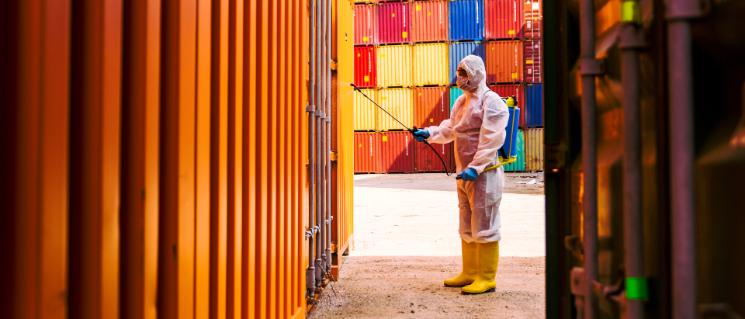
Global Trade
Supply chains in crisis
The coronavirus pandemic has been an unprecedented shock for global supply chains. How are they responding?
In December 2019, doctors in Wuhan, China, began to see patients with unusual and worrying symptoms. They suspected that the cases of respiratory problems and pneumonia appearing in their clinics were caused by a virus that hadn’t previously been seen in humans. On January 12, 2020, Chinese scientists published the genetic sequence of the new virus. The next day, health authorities in Thailand reported the first case of the new disease outside mainland China.
The next chapters of the COVID-19 story unfolded at frightening speed. When the city of Wuhan was placed under lockdown on January 23 in an effort to control the spread of the disease, World Health Organization officials described the move as "unprecedented in public health history.” Three months later, half the world’s population was being requested or required to stay at home as more than 90 countries introduced strict quarantine rules and movement restrictions. More than 2.7 million cases of the new coronavirus had been positively identified in 210 countries by the third week of April, and more than 190,000 people with the disease had lost their lives. With testing equipment and infrastructure in short supply around the world, officials believe that the true figures for both cases and deaths are much higher.
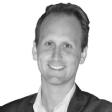
We are seeing disruption like nothing before,
Tobias Larsson - CEO, DHL Resilience360
Economic Impact
The new coronavirus has triggered much more than a health crisis. The pandemic has also had far-reaching effects on almost every part of the global economy. Companies have faced significant financial and operational challenges as they strive to keep producing through the crisis.
It has been a busy year for Tobias Larsson, CEO, DHL Resilience360, the cloud-based platform that helps companies to visualize, track and protect their business operations. Organizations in multiple sectors worldwide use the platform as a core element of their risk management, business continuity planning and crisis response activities.
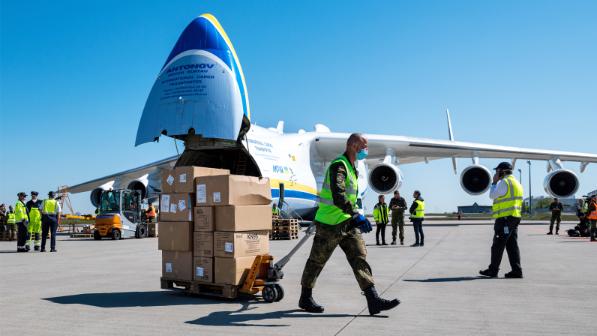
Larsson sums up the impact of the pandemic succinctly: “We are seeing disruption like nothing before,” he says. “First, you have a situation where companies need to protect their people from a potentially life-threatening disease. Then you have an issue with production and supply capacity, because businesses are being forced to shut down if they don’t produce essential equipment. And in addition, you have huge demand changes. Some sectors, such as automotive, have seen demand collapse, while businesses supplying products that aid the fight against the virus have seen it increase by as much as 800%.”
All those difficulties are compounded by the global reach of the crisis. “We have seen a number of major natural and man-made disasters over the last decade – from the earthquake in Japan in 2011 to the flooding in Thailand later the same year – which hit the technology sector particularly hard.” says Larsson. “But they were local or regional events that often had global effects.”
Today, he notes, demand and supply are being hit in almost every region. That makes it much more difficult for companies to execute their existing resilience strategies, which often rely on the ability to shift production around the globe and switch volumes between suppliers in different regions. “And the impact on different regions is not in sync,” adds Larsson. “So, when China was opening its factories again, their customers in Europe and the U.S. were still shut down.”
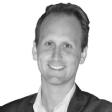
Our customers are preparing for an increase in the number of their suppliers experiencing financial difficulties over the coming months
Tobias Larsson - CEO, DHL Resilience360
Logistics Feel the Strain
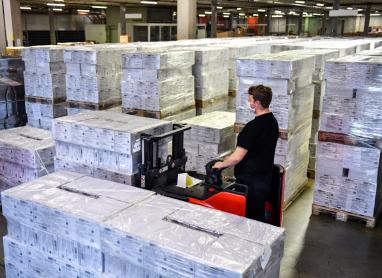
Smart logistics strategies are a critical part of many organizations’ response to disruptive events. The world’s transportation networks have proved extremely adaptable in previous crises, with carriers moving assets, altering routes and rapidly adjusting capacity to meet changing demand.
But the impact of COVID-19 has overwhelmed the ability of many logistics networks to respond, says Larsson. “In every other crisis, we say that suppliers are the critical link,” he says. “If they can produce, you can always find a way to deliver.”
This year, however, logistics links have been under unprecedented pressure. The collapse in air travel removed up to half the world’s normal air cargo capacity from the market, since much material moves in the bellies of passenger flights. Port closures and labor shortages slowed the movement of ocean freight. Trucking companies struggled to find drivers, and to overcome border delays and the closure of normal routes.
Even as operators and governments take action to improve flows and reopen key routes, returning services to normal will take some time. “Lots of important assets, from vessels to shipping containers, were stranded in the wrong place,” says Larsson. “Now operators need to try and restore a balance.
Want it Delivered?
Why go looking for the latest logistics stories and insights when you can have them delivered right to you?
Uncharted Waters
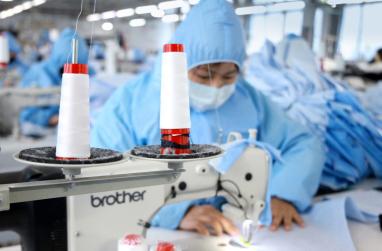
How have different organizations coped with this extraordinary combination of challenges? At the outset of the crisis, says Larsson, all businesses had one thing in common: They weren’t fully prepared. “This is absolutely a black swan event,” he notes. “Nobody could economically have put in place all the measures they might need to handle disruption on this scale.”
As a consequence, the pandemic has not just been a test of existing business continuity plans, but of a company’s ability to think and act on its feet. “Nobody could have planned for this particular crisis, but the most successful companies are those that had planned for other kinds of crisis,” says Larsson. “There are things that are common to an effective response in every crisis – like getting a task force together quickly; ensuring they can communicate effectively and have access to the right information to make decisions; ensuring they can move resources quickly and get funds to the parts of the business that need them. It really helps if you have done this before, if your people are trained in crisis response and have rehearsed these situations.”
On the ground, an unprecedented situation calls for innovative solutions. “We’ve seen examples all over the world of companies doing things they have never had to do before, and very quickly,” says Larsson. “Whether that is reconfiguring production lines so workers can operate at a safe distance from one another, or even retooling to make a completely different kind of product.”
Companies have been creative in finding solutions to their logistics challenges, too, says Larsson, whether that means teaming up with other firms to share the cost of an air charter, or switching to new routes and new transport modes. The Resilience360 team, meanwhile, has developed its own offerings to meet the needs of the crisis. “We are creating new analytics for our customers so they can track the direct impact of the changing situation on their supply networks,” he says. “Whether that’s local rules governing which business activities are permitted, or the status of critical routes and supply chain nodes.” The companies that benefit most from that approach, he adds, are those that have already built detailed maps of their networks, allowing them to monitor potential impact on the operations of second- and third-tier suppliers. Being better prepared has enabled some companies to avoid costs in the high double-digit or even triple-digit millions of euros.
The Road to Recovery
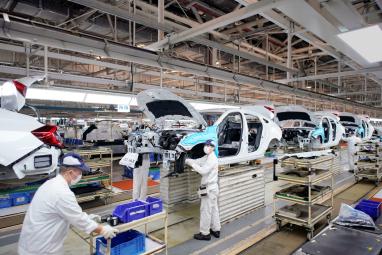
As governments around the world gradually began to lift virus-related restrictions, companies turned their attention to the post-crisis world. While the recovery phase of the crisis is unfolding at a slower, less breathless pace, it still involves plenty of uncertainty. Medical researchers still don’t know when effective treatments or vaccines will be available. Health authorities don’t know whether severe social restrictions will be needed to combat subsequent waves of infections. And businesses don’t yet understand the long-term impact of the crisis on consumer behavior or economic activity.
Consultants at McKinsey & Company are warning businesses that they need to prepare for multiple post-crisis scenarios, ranging from a relatively quick, V-shaped uptick in demand to a prolonged downturn. And the precise shape of the next normal will be region- and industry-specific. Some of the changes in customer behavior since the start of the crisis may turn out to be permanent.
Even if they enjoy healthy levels of demand, companies may not be able to operate their future supply chains in the same way. Despite their own best efforts and the availability of large-scale state support in many regions, not every company will have the financial strength to weather the current storm. “Our customers are preparing for an increase in the number of their suppliers experiencing financial difficulties over the coming months,” says Larsson. “So they are ramping up their supplier monitoring activities and looking closely at financial results and other signs of distress, such as media reports of workers being laid off.”
Organizations will be closely scrutinizing the overall resilience of their supply chains, too, with companies rethinking everything from the size and distribution of finished goods inventories to their exposure to specific suppliers, customers or industry segments. “In such uncertain times,” Larsson concludes, “nobody wants too many of their eggs in one basket, especially if that basket is far away in another part of the world.”
Published: June 2020