With operations in 55 countries, more than 140,000 employees and customers in industries from fashion and retail to chemicals and energy, it is little surprise that different parts of DHL’s Supply Chain business felt the impact of the COVID-19 pandemic very differently. “We have seen a very schizophrenic response across our operations,” says Oscar de Bok, a logistics industry veteran who has worked at DHL Supply Chain for more than 20 years and has held the top job since 2019.
“On the one hand, we have sectors like healthcare, consumer goods and grocery retail where we have seen huge volumes and the need to ensure the supply of essential goods. On the other, there are industries like automotive or the fashion and luxury sector where factories closed down. We had to find a way to temporarily shut our facilities while still keeping everything ready to support those customers when things reopen again.”
Safety is paramount
With the economic fallout of the virus pulling the business in different directions, the organization has had a singular focus throughout the crisis, says de Bok: “We needed to keep our people safe, looking after them so they could continue to deliver for our customers.”
DHL’s global footprint meant that it had an early warning of what would be required to achieve those objectives. “At the beginning of the outbreak, our partners at SF DHL Supply Chain in China did great work developing operating procedures to work safely and efficiently,” says de Bok. “We then further built on that creating robust processes at our facilities in Singapore. Then, as the pandemic spread, we could quickly replicate those procedures, along the way adding new best practices from country organizations around the world.”
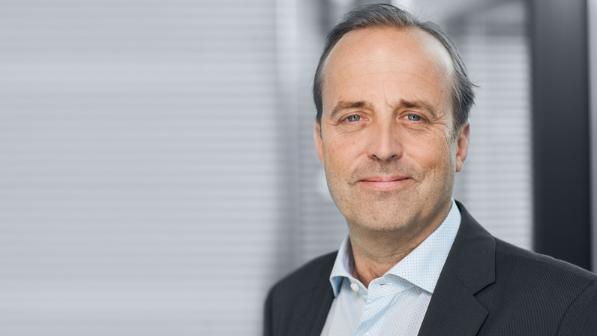
Adapting a supply chain logistics operation to work safely in a pandemic requires a host of actions, explains de Bok, including the provision of personal protective equipment, adjusting the number of personnel at each site and introducing new split shift systems with rigorous separation of teams. All those changes had to be made in close collaboration with customers and with health authorities in every region.
The structure of many supply chain logistics operations also had to change, says de Bok, with some segments opening new warehouse locations to cope with radically increased volumes of certain items, or to temporarily hold inventory that could no longer flow to end users. “This is where our focus on training and standard operating procedures has really come into its own,” he says. “We were able to re-allocate people and space very quickly.”
Digital dividend
Technology helped too. The business has been pursuing a sophisticated digital strategy for several years, and those capabilities have shown their worth during the pandemic, says de Bok. “We have spent a lot of time developing our data and analytics capabilities, and that has dramatically improved visibility across our operations,” he says. “That data was critical to support our decision-making in the crisis: We could immediately see where we had capacity and how we could move resources to keep operations running and meet our customers’ needs.”
The robots that operate in many DHL warehouses around the world are also helping facilities to run efficiently when social distancing rules for employees are in place. “We have maintained the momentum of our digital transformation despite the crisis,” says de Bok, noting that hundreds more robots will be deployed at DHL facilities in the coming months.
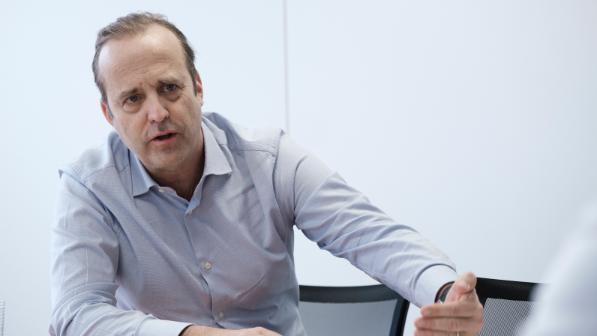
While rigorous standards, data and automation were critical, crisis conditions call for human ingenuity too. Around the world, DHL was involved in completely unprecedented projects, many requiring complex supply chain operations that needed to be built in just a few days. The organization helped health authorities in Italy and the U.K. to build and equip emergency field hospitals, for example, and to ramp up new manufacturing supply chains for the production of thousands of ventilators. In the U.S., DHL Supply Chain activated its existing volunteer program to support its partner, the American Red Cross. In April, the division sent forklift certified employees to the American Red Cross Disaster Response Warehouses in Atlanta (Georgia) and Carlisle (Pennsylvania) to assist with the logistics and handling of personal protective equipment and other supplies, needed to support the nation’s blood drive program in response to the spread of COVID-19. In Australia, the company worked with grocery retailer Woolworth to pack and deliver thousands of “basics boxes” of food and essential items for vulnerable people who could not leave their homes to shop. In Brazil, cosmetics giant L’Oréal converted production lines to make hand gels and other critical hygiene products, which DHL teams distributed to people in the Favelas of Rio de Janeiro. The wider DHL family supported COVID-19 response efforts by sending DHL Disaster Response Teams (DRT), comprised of specially trained employees, to assist the Costa Rican national emergency response organization with setting up a warehouse to manage the logistics for COVID-19 related supplies. A DRT also supported the Colombian Red Cross in Bogota by coordinating the delivery of 4,000 boxes of food to those in need, and the team utilized a DHL Express facility to assemble an additional 21,000 food ration bags to be delivered to affected families. And in Poland, DHL Supply Chain donated materials to enable the production of 40,000 face shields using 3D printing technology.
Why go looking for the latest logistics stories and insights when you can have them delivered right to you?
A mission becomes alive: Connecting People – Improving Lives
Those examples, says de Bok, are just a few of dozens of similar efforts underway across the DHL Supply Chain network. They were only possible, he adds, because team members on the ground were willing to make them happen in challenging times. “In our healthcare sites in the Netherlands, I’ve seen at first hand how dedicated our people are in this situation,” he says. “Our teams know they are performing a vital role. Their passion and can-do attitude has made all the difference in this crisis.”
The picture is the same around the world, he adds. When Singapore closed its border with Malaysia early in the crisis, two hundred employees who normally commute between the countries agreed to stay in Singapore to support customer operations there, even though that meant separation from their families. In Spanish warehouses, staff have been applauding at the end of their workday to welcome the arrival of their colleagues in the next shift.
As economies begin to open up again, what can DHL and its customers learn from their experience of this crisis? “Nobody can claim they were fully prepared for this,” says de Bok. “Like everyone else, we had to work hard to introduce new processes and get the materials we needed to protect our people. I think every organization is going to rethink their emergency response and business continuity planning.” Most importantly, however, de Bok believes that the crisis has shown the value of collaboration across the supply chain. “We overcame challenges in partnership with our customers. It takes flexibility and a willingness to act on both sides to create solutions to difficult problems. With many of our customers, I believe that our teamwork during this time sets a template for closer, more productive relationships in the future.” — Jonathan Ward
Published: May 2020
Images: DHL