The leading edge of technology sometimes takes you in unexpected directions. At the beginning of the 20th century, Count Ferdinand von Zeppelin was convinced the airship would be the key to future fast, comfortable and efficient mobility. Zeppelin chose a plot of land outside the city of Friedrichshafen, Germany, as the production base for his endeavors, using the sky above Lake Constance as a testing ground for prototypes.
By 1915, the city had become a hub for aviation innovation, with hundreds of engineers working to make Zeppelin’s vision a reality. The airships were performing well, but one stubborn issue threatened their wider uptake: noise. The relatively primitive gearboxes between the fast-spinning engines and slow-turning propellors were so loud that Alfred Colsman, general manager of the business, described the sound in the main gondola of a craft as “almost unbearable.”
The search for a solution led Colsman and his colleague Alfred von Soden-Fraunhofen to the work of Swiss engineer Max Maag, who had devised a way of manufacturing high-precision gears. The three men entered an agreement to license Maag’s technology in Germany, establishing a new business called Zahnradfabrik Friedrichshafen GmbH close to the Zeppelin plant.
ZF, as the company became known, quickly found plenty of willing customers beyond the airship industry. Quiet, efficient gears were in demand across a wide range of sectors – including boats, agricultural machines and the fast-growing automotive industry. It was the last of those that came to dominate the company’s future. By the end of the century, ZF had evolved into one of the world’s major automotive suppliers, producing advanced transmission systems for cars, trucks and buses.
From smoother to smarter
Today, five years into its second century of existence, ZF is mid-way through another major transformation. The company that built its fortunes on excellence in mechanical design and production is looking for a dominant role in electronics, sensors and software.
As in its earliest days, ZF’s reinvention has been led by a desire to address its customers’ biggest challenges. The 2015 acquisition of U.S.-based TRW gave the company access to its portfolio of chassis and safety technologies, which complement its traditional powertrain expertise. It launched a dedicated e-mobility division in 2016, with a mission to develop motors and transmission systems for hybrid and fully electric vehicles. Two years later, ZF announced a new strategy, aiming to position itself as a key provider of “next-generation mobility” solutions, including technologies for autonomous and shared vehicles alongside its EV and hybrid offerings.
Shifting the primary expertise of an organization from metal to silicon is a hugely demanding undertaking, requiring new engineering, manufacturing and testing capabilities. It also requires the development of an entirely new supplier ecosystem.
ZF has incorporated electronics into its products for many years, says Janine Montforts, the company’s Director Advanced Technology Procurement ADAS (advanced driver-assistance systems). She leads a specialist team set up to help the company build the technology supply base it needs to support its ambitions in autonomous and assisted driving.
But the challenges of advanced driving systems have dramatically altered the scope of its requirements. “In the past, we would ask our suppliers to provide, say, a simple electronic chip,” she says. “Today, we are buying a package that includes the chip along with a lot of associated software, it’s a much more complex proposition.”
The company is working with aggressive timescales, too. Fully autonomous passenger cars are still some years away, although many of ZF’s customers in the passenger car sector are currently offering Level 2 automation systems, which take over many driving functions while still requiring the driver to keep their hands on the wheel. Yet other mobility sectors are pushing forward much faster: “We believe that over the next decade, autonomous shuttles will become widely used in public transport systems – including airports, park-and-ride schemes and inner cities. “These types of vehicles will make a public transport system without timetables a possibility and will redefine urban mobility,” says Montforts. ZF already offers autonomous shuttles today via its subsidiary 2getthere, which has successfully been running driverless shuttles on restricted routes for more than 20 years. Vehicles supplied by 2getthere have covered more than 100 million kilometers autonomously, transporting more than 14 million passengers with a system availability of over 99%.
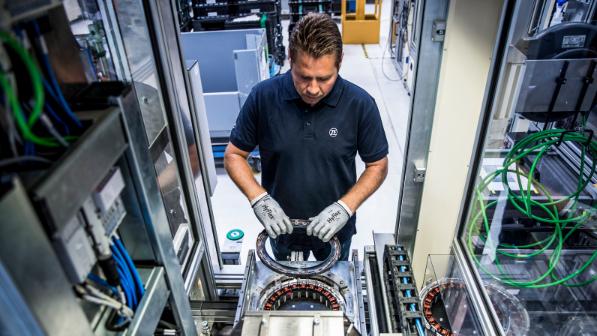
The rapid pace of development places new demands on supplier relationships, says Montforts. “When you work with traditional automotive suppliers, they are used to long development cycles, with maybe four years between the start of a project and full-scale production. In autonomous driving we are in a world where the automotive computing power available even two years ago was regarded as sufficient but already today is requiring further upscaling. Innovation cycles are much shorter and you need to be always on the lookout for the next technological game-changer.”
Why go looking for the latest logistics stories and insights when you can have them delivered right to you?
Growing up fast
Then there is the challenge of working with young, highly innovative companies. The autonomous driving sector is so new, says Montforts, that many potential suppliers “still have a startup mentality.” Beyond identifying the most promising suppliers, much of the work of the Advanced Technology Procurement Group is about ensuring these companies can meet the exacting quality and delivery requirements of the automotive industry.
Component and systems suppliers like ZF are a critical link in the automotive sector’s lean, just-in-time supply chains. “In our business, there is no leeway,” says Montforts. “You can’t miss a delivery to your automotive customer and just assume it will be okay to fill your order the next day.”
It isn’t just small startups that face a steep learning curve if they want to supply the automotive sector. Plenty of high-tech products come from the industry giants that also provide critical components for computers, phones and countless other product sectors. For these companies, says Montforts, the growing importance of the automotive market is encouraging a shift in attitudes.
“I started working in automotive electronics in 2002, and back then the sector was less than 5% of the high-tech market – for some suppliers even less than 1%. We were a ‘nice-to-have’ customer, not a critical one.” Today, she says, big technology players value their automotive customers because they offer significant volumes and valuable stability. “Companies recognize that if they secure business with us, they will have that business for four or five years, which is the usual lifecycle of an automotive product.”
Leveling up
ZF’s push to the leading edge of autonomous driving is already winning customers. In August, for example, the company began the volume production of advanced solid-state LiDAR systems, which allow vehicles to construct a real-time, 3D model of their surroundings. The new sensors will start to appear on passenger cars in 2022.
How long, then, before the industry achieves Level 4 or 5 autonomy, the point at which cars and trucks can really drive themselves in some (Level 4) or all (Level 5) conditions? “From a technical perspective, we’re ready to go. The technologies needed – in particular radar, LiDAR and camera systems – are sufficiently advanced, and our central computer ZF ProAI can even manage complex maneuvers,” says Montforts. “But in lots of countries, we still don’t have a standardized infrastructure and legislation that would allow autonomous vehicles to operate in normal traffic.”
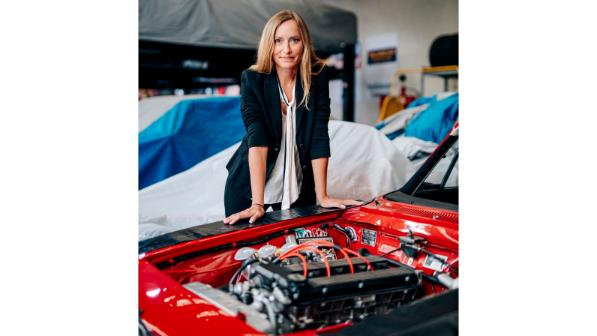
Driving a vehicle safely in real-world conditions is a hugely complex task, too difficult for conventional, rule-based computer programming. Every major player in the sector uses AI technologies, with deep-learning models that must be trained through exposure to millions of real or simulated driving events. “Technically, training is the limiting factor right now,” says Montforts. “But the timescale for autonomy will also be governed by regulations, and of course by the economic case.”
For ZF, developing technologies for innovative and as yet unproven forms of transport is nothing new, of course. “One of the best things about working here is the willingness to take a long-term view, says Montforts. “With e-mobility, we spent many years developing our position, and we have reached the point where we are no longer developing new products for combustion engine vehicles. Now we are taking the same approach with autonomous driving.”
For Montforts, the opportunity to spend time working at the forefront of a new technological revolution is thrilling. “For me, it’s a bit like the introduction of the internet,” she explains. “You know you are working on something that could eventually change the world.” But if working with supercomputers and AI systems ever gets too much, she can ground herself in old-school automotive technology at home, working on her historic VW 181 Thing. “It’s bright orange,” she says, “and the battery is just about the only electrical thing on it.” — Jonathan Ward
Published: December 2020
Images: Thomas Pirot for DHL Delivered.; Dominik Gigler/ZF