The sirens never stopped. From February onward, the small Italian city of Bergamo was hit by the then-novel coronavirus that would later surge across the world. On March 10, the city, nestled at the foothills of the Italian Alps, went into lockdown.
“It was eery,” says Francesco Capelli, Operations Director at Bergamo Hub. “Our city was virtually silent. All we heard were announcements made from military vans to stay indoors, and the sound of ambulances every three to four minutes.”
With Bergamo’s citizens staying indoors, the streets were deserted. DHL vans were on the road, however. “Traditionally, in any crisis, DHL has a policy of last out, first in,” says Alberto Nobis, CEO Europe, DHL Express, himself an Italian, who has been working in agile mode in northern Italy since the start of the pandemic. “Even in wars or major natural disasters like the Icelandic ash cloud in 2010 or the 2018 hurricanes in the Caribbean, we are known for not giving up and doing what we can. This time we were never out. After a short period of reorganizing themselves, our teams kept on going at double speed, even under very difficult conditions.”
At the center of the crisis
In early February, as the pandemic took hold in northern Italy, Bergamo Hub (BGY) – a key part of the DHL Express network – went into overdrive, as did its hub in nearby Milan (MXP). Teams worked day and night to receive, process and deliver personal protective equipment (PPE), respirators, critical medicines and also general e-commerce goods for businesses and private individuals across Italy. Yet it was becoming apparent that the virus was spiralling out of control in Bergamo, and that if one person working at the hub became infected, it would quickly spread among teams. So on February 20 – when to most of the world COVID-19 was still an obscure threat rather than headline news – Jesus Sanchez, MD Hubs and Gateways Italy, took the decision to tell some 400 customs department, back office and support function staff at Bergamo Hub to work from home. After that around 400 operations employees (warehouse and ramp agents) were sent home and temporarily stopped work. “This was an unprecedented and unusual move and the decision wasn’t taken lightly, because it was a massive logistical challenge,” says Sanchez. Nevertheless, it was a decision that undoubtedly saved lives.
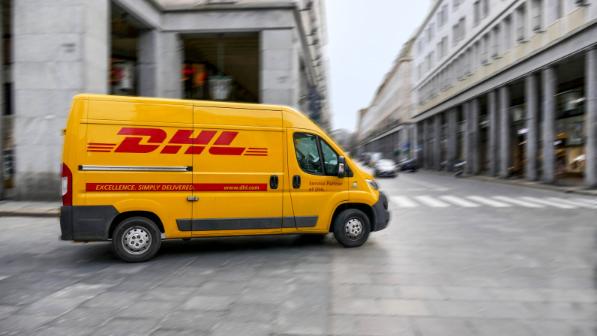
At peak times, BGY handled 50,000 air shipments from Europe and around the world every day. While volumes initially dropped, both hubs and service centers had to prepare entirely new routines and source masks, gloves, hand sanitizers, disinfectants and laptops for teams working from home.
Working to deliver – 24/7
Whether at home or carrying out critical tasks at the hubs and service centers, or, of course, delivering to customers, teams stepped up, organized themselves and, in many cases, even reported for work after losing close relatives. All were regularly updated about the situation on the ground and received links to videos on how to cope in lockdown that had been recorded with a psychologist. “Some people call working from home ‘smart working,’” says Sanchez. “I call it ‘safe working.’ I truly believe the action we took saved lives.” Normally, customers could expect their cargo to clear customs and be delivered overnight or within 24 hours. Despite these extraordinary circumstances, Sanchez is proud to say that average delivery time increased to just 48 hours, such was the dedication of the customs team.
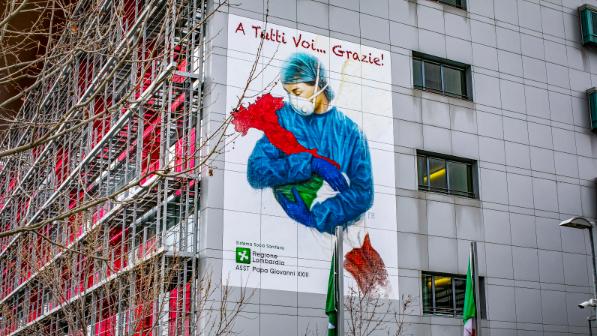
Motivated to overcome all challenges
“At first, members of the customs team were concerned about how they would cope with home working,” says Maria Caterina Benincasa, Import Supervisor, Customs Department, Bergamo Hub. “However, these worries disappeared in the blink of an eye because a huge increase in COVID-related shipments – such as masks and other PPE items, coronavirus tests and ventilators – began pouring into the hub. It was critical that this essential life-saving equipment cleared customs, and we were the ones who had to make sure it happened. That was our motivation, our energy. Suddenly everyone in the department found a new willingness to keep going, to keep working, and find their own solutions to the personal challenges they were facing.” Yet this was no easy task, because the volume of goods needing to clear customs was huge. From January to May 2020, the hub registered a 115% increase in imports of medical devices on the previous year. To complicate matters, the team was also having to deal with constantly evolving Italian customs legislation relating to medical devices, which changed 14 times in three months.
Finding the strength to keep going
Those remaining at the facilities in the Bergamo area faced the daunting task of having to ensure teams were adequately protected from the virus. It was also crucial to protect the mental wellbeing of employees in a harrowing situation where approximately 15,000 of Bergamo’s 120,000 inhabitants had contracted coronavirus and more than 6,000 had died. “At first I was scared,” admits Matteo Camozzi, Operations Supervisor at Bergamo Service Center. “But what kept me going, and all of my colleagues too, was the need to help others. We knew that Bergamo hospital, as well as hospitals, doctors, citizens and customers all across Italy, were relying on our deliveries. Personally, I also have a very strong faith, and that sustained me throughout this crisis.”
One man who was never afraid is Alessandro Caironi, a senior ramp supervisor who says his faith gave him a lot of strength. He also credits the strength that people from Bergamo are known for throughout Italy as part of what made teams so resilient. “Throughout history, there has been a special spirit in Bergamo – we are mountain people, used to defending ourselves, but we are also known for being very kind and helpful,” he comments. “This is the spirit that kept us going and also kept us going the extra mile at work, no matter what.”
A new way of working
“Since the COVID-19 crisis we have had to modify our entire European and global network in ways that would normally have taken five years of planning and evaluation,” says Roy Hughes, EVP Network Operations & Aviation, DHL Express Europe. “At the start of the pandemic, there were several weeks where our planes were the only ones flying around the world. As passenger airlines became grounded, we had to find other ways of making up for cargo capacity we normally use for a part of our Express shipments, such as securing extra charters, which we managed, albeit at high cost.”
Alberto Nobis believes that DHL has emerged with clear priorities and a new way of working. “First and foremost are the safety and wellbeing of our teams because that’s also what guarantees our continuity,” he says.
“Next is technology. Initially, our tech platform supported 10,000 remote workers, but today there are more than 200,000.
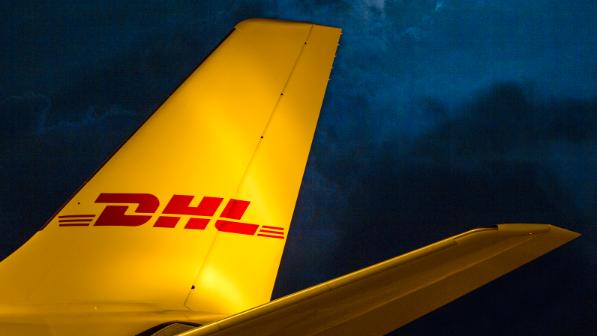
“Digitalization was something we were focused on before the crisis, but this has been accelerated and we are now helping many of our customers transfer their business online. Technology and digitalization will be essential to improving both our offering to customers and the work of our employees.”
Nobis concludes: “Even though these are turbulent times, we are confident we will grow in the future. Despite a significant drop in our volumes at the beginning of the pandemic in April, we quickly saw a great recovery in our shipment volumes from mid-May on. Currently we are growing at high single-digit rates and all trends seem to be converging toward a record high peak period from now until year-end.
Why go looking for the latest logistics stories and insights when you can have them delivered right to you?
Investing in the future
In Italy, this growth will also come from a facility at Milan Malpensa. The company is investing in a new hub that started operations in September and will soon become a crucial part of DHL Express’ European network, with the eventual capacity to increase to 1,300 employees and flights linking Europe, the U.S. and the Middle East.
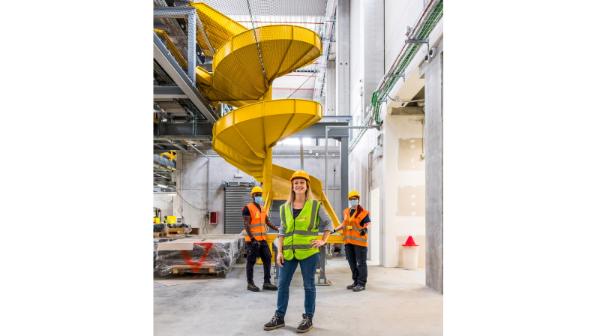
“Italy is an important European center for Manufacturing, Agriculture, Life sciences & Healthcare, Automotive and Fashion, so there is a high volume of exports from the country itself,” says Nobis. “However, our new Malpensa Hub will also be connected to our global hubs: CVG in Cinncinatti, U.S., and BAH in Al Muharraq, Kingdom of Bahrain.”
“Malpensa offers us opportunities to expand services that are critical to us absorbing our expanding volumes and securing the future,” says Nobis. “Bergamo has been key to our Italian operations for two decades, but due to its limited single runway and geographic location in an Alpine region, we are unable to expand as we need. Despite this, together with our gateway in Brescia, Bergamo is a key part of our ‘family’ in northern Italy. La Famiglia – ‘family’ – is everything in Italy, and as one DHL family, with Malpensa, Bergamo and Brescia, we are confident that we can master the future and deliver for our customers, deliver growth and deliver a secure future for our teams.” — Michelle Bach
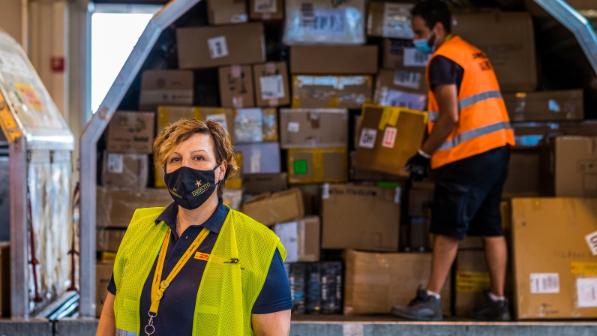
Published: October 2020
Images: Mario Rota for Delivered;
Antonello Marangi/Alamy/mauritius images; ddp; DHL; private
Production Milan/Bergamo: Valentina Gradoli