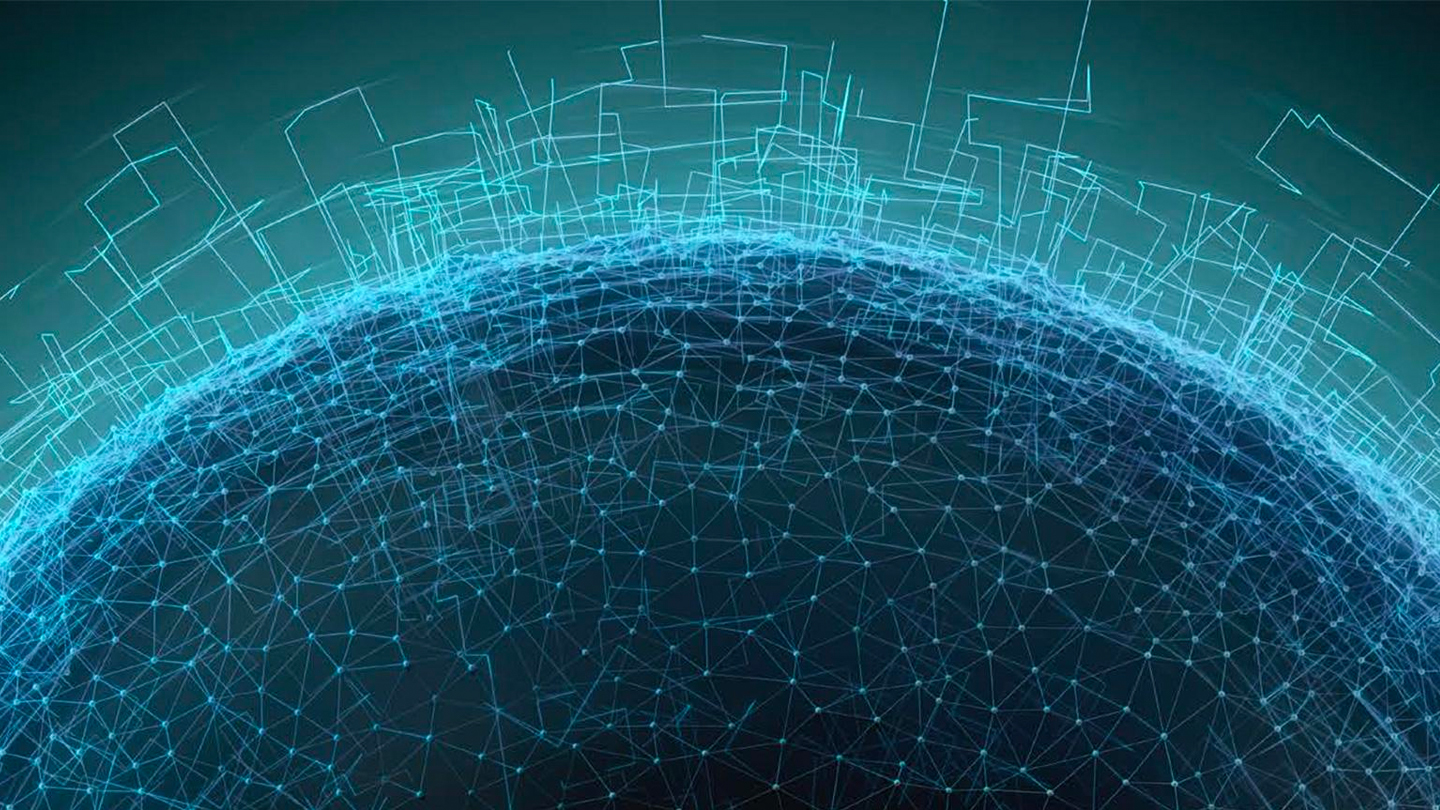
Press Releases
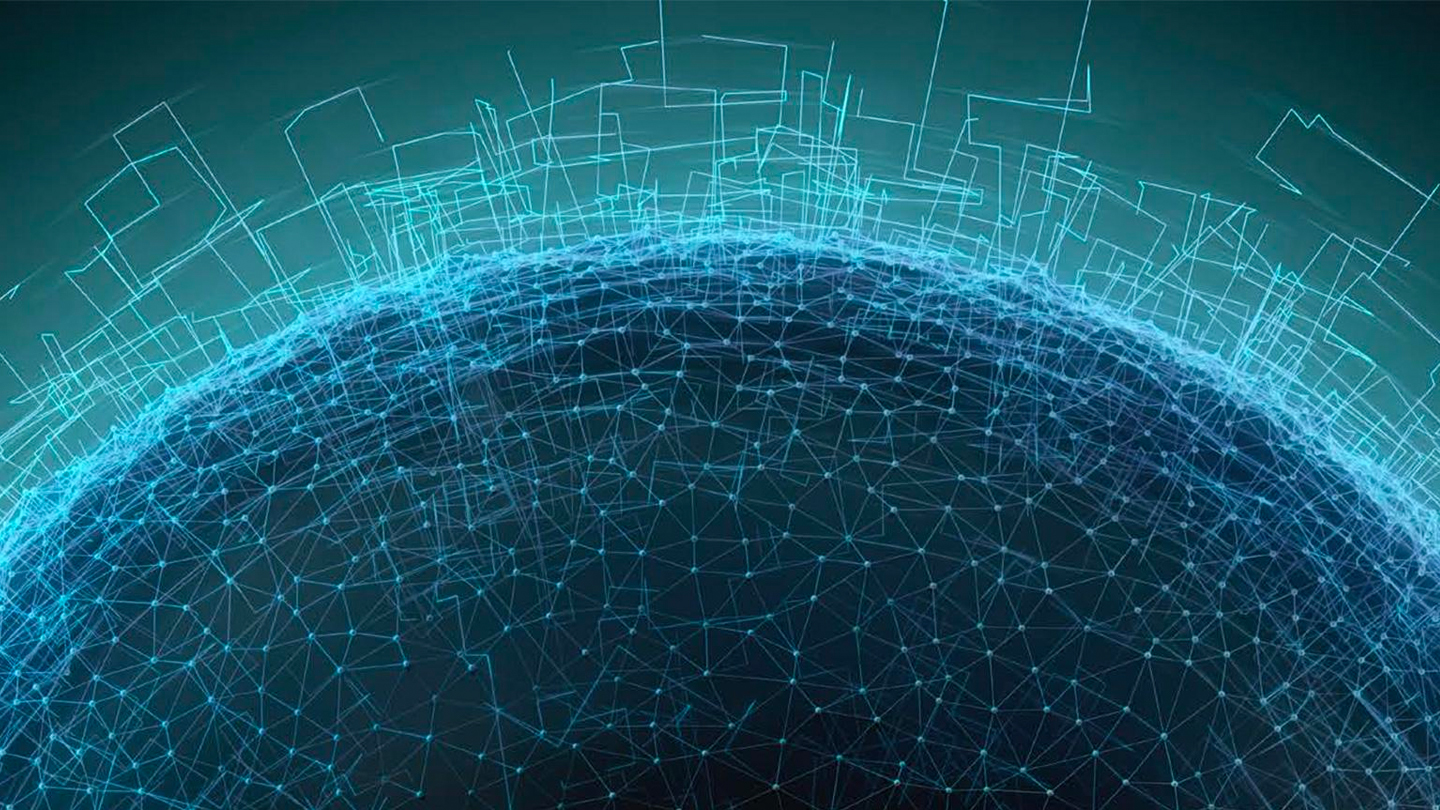
Global Press Releases
Discover all the latest global news from DHL by taking a look at our recent global press releases
Media Center
This resource center for journalists housing our latest global press releases, useful multimedia materials, a list of press events and a direct link to our spokespersons.