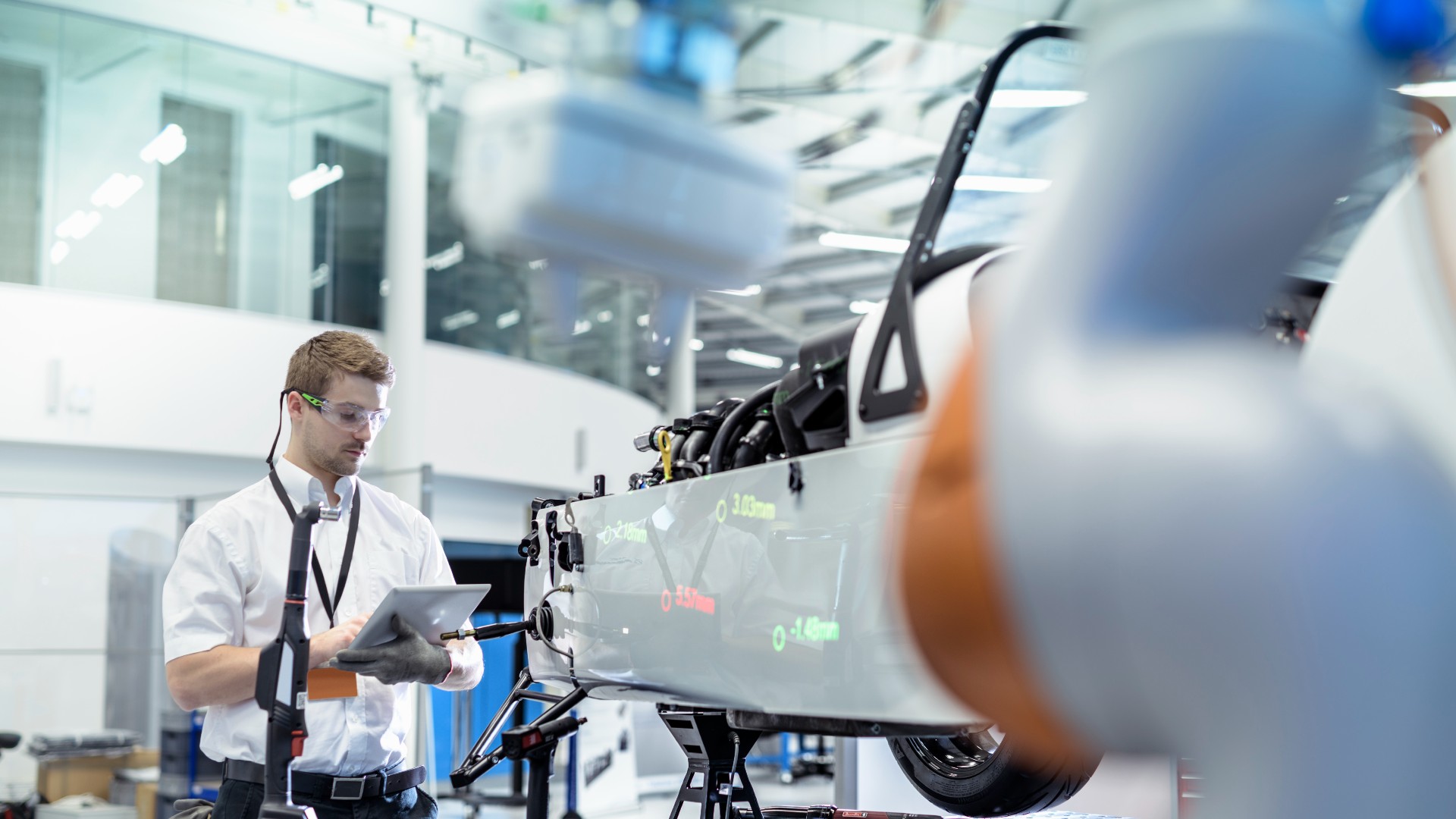
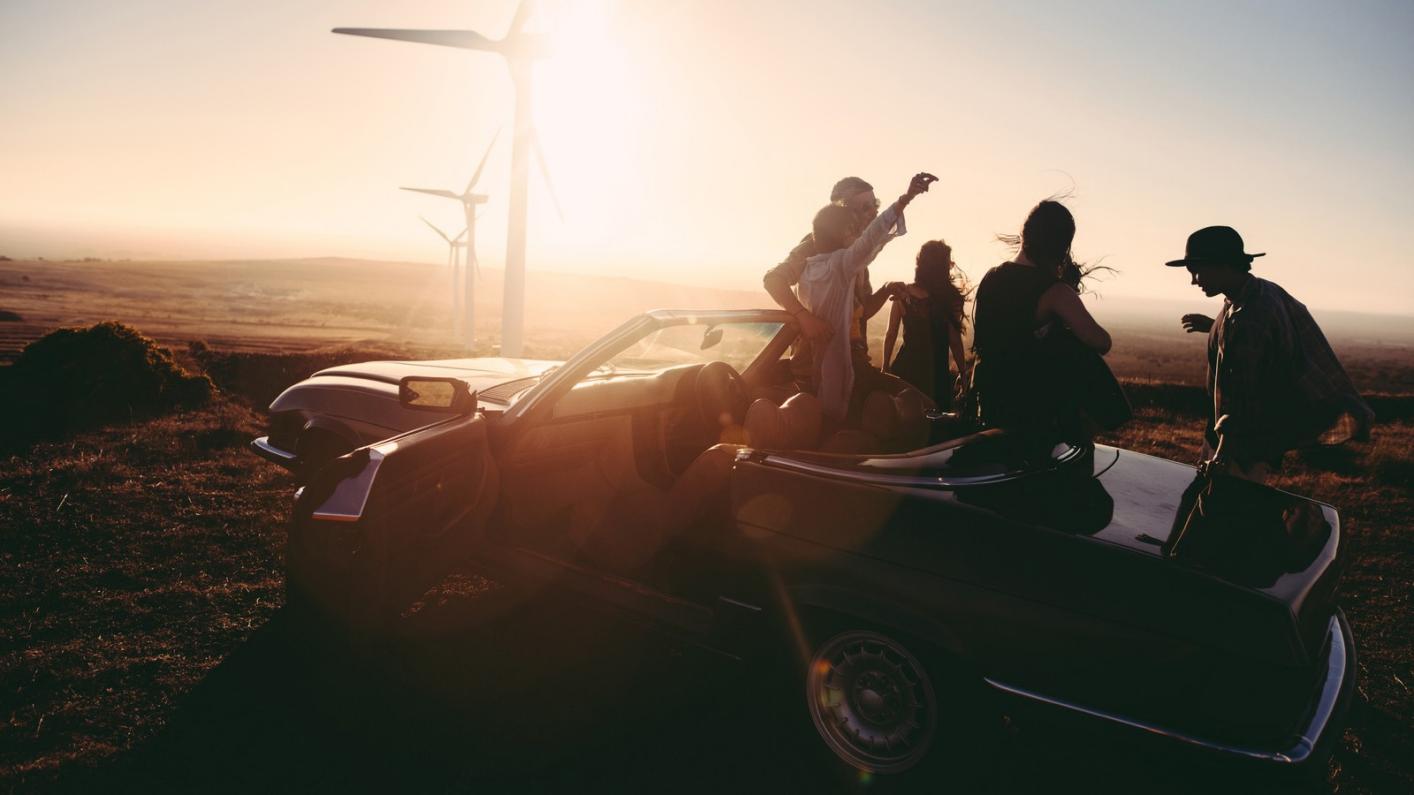
Auto-Mobility Logistics
We never stop delivering excellence in automotive logistics
The Next Stop in Automotive Logistics
The Auto-Mobility sector is adapting and rethinking its current supply chain infrastructure. Production is moving closer to consumption, new players are entering the market to support vehicles built on semiconductor technology, and OEMs are investing heavily in mega-factories in emerging markets.
As a specialist in all aspects of Auto-Mobility and automotive logistics, DHL focuses on tires, components, passenger vehicles, commercial vehicles, and aftermarket. We are committed to supporting the auto logistics sector by providing valuable services, from mitigating value chain disruptions to enabling automotive electrification.
With a globally recognized track record of delivering exceptional international auto logistics, global access, and industry-advancing innovation, you can be sure DHL will always evolve with you.
10 million
EV batteries Delivered in 2021
15,000
Auto-Mobility Supply Chain Experts
1,000
Service Logistics Operations in 140 Countries
110 million
Tires Transported Annually
Trending Topics
Explore the trends and developments that are impacting supply chains and reshaping the automotive logistics sector.
DHL EV TV Series
A brand-new series exploring the future of Electric vehicles
Discover Our Upcoming Auto-Mobility Events
Experience the events that are shaping the future of auto logistics. We look forward to welcoming you.
Vehicles, Tires, Components and Aftermarket
Essential automotive and sector services from the leaders in Auto-Mobility logistics.
Component Manufacturers
Our Auto-Mobility inbound-to-manufacturing service optimizes assembly lines while satisfying cost-saving requirements and parts dependability. Services such as in-plant logistics, sequencing, and just-in-time delivery ensure operations efficiency. We also focus on supplier visibility and management, collection, and consolidation services for I2M, emergency shipments, product type-tailored logistics, and risk management.
We are specialists in battery logistics, smart monitoring, data analytics, rapid adaptation, and separating logistics expenses from parts costs: a truly global supply chain solution for the Auto-Mobility components sector including independent aftermarket distribution and e-commerce. We ensure that time-critical deliveries are made on schedule to maintain production, fulfill manufacturing objectives, and meet customer needs.
Tires
Tire demand can be volatile; consumers expect rapid product availability while Auto-Mobility providers need to minimize inventory. We assist by providing raw material inbound solutions, finished product distribution centers, flexible deliveries, and customized tire warehouse management systems.
At DHL, we understand that specific needs require specialized knowledge and solutions that are right for the customer. We invest in developing innovative expertise and systems to ensure maximum flexibility and technical advantages such as smart containers. Tire manufacturers are now less reliant on wholesalers and with the support of logistics can establish direct-to-market channels. This means true local, global, and sustainable end-to-end solutions, providing OEM manufacturing support from tire logistics specialists.
Passenger Vehicles
To meet the demand for new vehicle launches, electric vehicles, personalization, connected cars, competitive prices, and high quality and reliable support, DHL offers many supportive services, including finished vehicle logistics and taking over responsibility for your whole supply chain as your lead logistics partner (LLP).
DHL is a global leader offering integrated, reliable, and flexible end-to-end passenger vehicle logistics solutions including data systems, predictive analytics, and inventory management. Our industry experts can provide LLP/control tower-based end-to-end visibility and optimization.
Advanced services include our bespoke inbound-to-manufacturing solutions supported by a highly effective global network to guarantee ‘on-time’ delivery of parts to manufacturing centers through extensive use of just-in-time and just-in-sequence management systems. We also provide in-plant services, packing and kitting (KD), utilizing pioneering supply chain management tools and customized aftermarket storage and distribution solutions.
We help our customers to keep up with the increase in new vehicle launches, product demand flexibility, global sustainability requirements, and the drive for electric vehicle transformation.
Commercial Vehicles
Environmental concerns, a drive to improve fuel efficiency and safety, and meeting vehicle regulations and certifications are key factors shaping future business decisions. We provide commercial vehicle supply chain services and logistics guidance to overcome challenges and achieve business-critical objectives.
We offer integrated, reliable, and flexible end-to-end commercial vehicle logistics solutions including data systems, analytics, and inventory management. Our industry experts can provide LLP/control tower-based end-to-end visibility and optimization.
Advanced services include our bespoke inbound-to-manufacturing solutions supported by a highly effective global network to guarantee ‘on-time’ delivery of parts to manufacturing centers through extensive use of just-in-time and just-in-sequence management systems. We also provide in-plant services, packing and kitting (KD), utilizing pioneering supply chain management tools and customized aftermarket storage and distribution solutions.
Aftermarket
Aftermarket services are a challenging and vital link in the automotive value chain. Expected to be worth $559 billion globally by 2030, the Aftermarket parts logistics market is rapidly changing. Supplier disruptions, increased competition, downward cost pressure, the rise of e-commerce and vehicle electrification are just some of the trends impacting parts and service suppliers.
Aftermarket services demand the highest levels of supply chain excellence; consumer expectations are high and failure to deliver can risk brand reputation. Our sustainable solutions minimize complexity and improve both visibility and control, to reduce lead times for the delivery of components to dealers globally.
Our dedicated and multi-user warehousing and transport solutions combine strategic thinking and operations excellence. We offer flexibility, based on need, from container management; local and regional distribution centers; and a dedicated transport network that provides delivery options ranging from economic overnight services to same-day deliveries.
Component Manufacturers
Our Auto-Mobility inbound-to-manufacturing service optimizes assembly lines while satisfying cost-saving requirements and parts dependability. Services such as in-plant logistics, sequencing, and just-in-time delivery ensure operations efficiency. We also focus on supplier visibility and management, collection, and consolidation services for I2M, emergency shipments, product type-tailored logistics, and risk management.
We are specialists in battery logistics, smart monitoring, data analytics, rapid adaptation, and separating logistics expenses from parts costs: a truly global supply chain solution for the Auto-Mobility components sector including independent aftermarket distribution and e-commerce. We ensure that time-critical deliveries are made on schedule to maintain production, fulfill manufacturing objectives, and meet customer needs.
Tires
Tire demand can be volatile; consumers expect rapid product availability while Auto-Mobility providers need to minimize inventory. We assist by providing raw material inbound solutions, finished product distribution centers, flexible deliveries, and customized tire warehouse management systems.
At DHL, we understand that specific needs require specialized knowledge and solutions that are right for the customer. We invest in developing innovative expertise and systems to ensure maximum flexibility and technical advantages such as smart containers. Tire manufacturers are now less reliant on wholesalers and with the support of logistics can establish direct-to-market channels. This means true local, global, and sustainable end-to-end solutions, providing OEM manufacturing support from tire logistics specialists.
Passenger Vehicles
To meet the demand for new vehicle launches, electric vehicles, personalization, connected cars, competitive prices, and high quality and reliable support, DHL offers many supportive services, including finished vehicle logistics and taking over responsibility for your whole supply chain as your lead logistics partner (LLP).
DHL is a global leader offering integrated, reliable, and flexible end-to-end passenger vehicle logistics solutions including data systems, predictive analytics, and inventory management. Our industry experts can provide LLP/control tower-based end-to-end visibility and optimization.
Advanced services include our bespoke inbound-to-manufacturing solutions supported by a highly effective global network to guarantee ‘on-time’ delivery of parts to manufacturing centers through extensive use of just-in-time and just-in-sequence management systems. We also provide in-plant services, packing and kitting (KD), utilizing pioneering supply chain management tools and customized aftermarket storage and distribution solutions.
We help our customers to keep up with the increase in new vehicle launches, product demand flexibility, global sustainability requirements, and the drive for electric vehicle transformation.
Commercial Vehicles
Environmental concerns, a drive to improve fuel efficiency and safety, and meeting vehicle regulations and certifications are key factors shaping future business decisions. We provide commercial vehicle supply chain services and logistics guidance to overcome challenges and achieve business-critical objectives.
We offer integrated, reliable, and flexible end-to-end commercial vehicle logistics solutions including data systems, analytics, and inventory management. Our industry experts can provide LLP/control tower-based end-to-end visibility and optimization.
Advanced services include our bespoke inbound-to-manufacturing solutions supported by a highly effective global network to guarantee ‘on-time’ delivery of parts to manufacturing centers through extensive use of just-in-time and just-in-sequence management systems. We also provide in-plant services, packing and kitting (KD), utilizing pioneering supply chain management tools and customized aftermarket storage and distribution solutions.
Aftermarket
Aftermarket services are a challenging and vital link in the automotive value chain. Expected to be worth $559 billion globally by 2030, the Aftermarket parts logistics market is rapidly changing. Supplier disruptions, increased competition, downward cost pressure, the rise of e-commerce and vehicle electrification are just some of the trends impacting parts and service suppliers.
Aftermarket services demand the highest levels of supply chain excellence; consumer expectations are high and failure to deliver can risk brand reputation. Our sustainable solutions minimize complexity and improve both visibility and control, to reduce lead times for the delivery of components to dealers globally.
Our dedicated and multi-user warehousing and transport solutions combine strategic thinking and operations excellence. We offer flexibility, based on need, from container management; local and regional distribution centers; and a dedicated transport network that provides delivery options ranging from economic overnight services to same-day deliveries.
Case Studies
Review a range of in-depth automotive logistics case studies and discover practical examples of how we helped our customers to stay ahead of the curve.
Additional Focus Areas
Fleet Management
DHL is the leading authority on maximizing the value and lifecycle of automotive logistics and transportation assets through best practice fleet management, improved efficiency, cost reduction and compliance with government regulations.
Sustainability
Our specialists deliver innovative and sustainability-motivated automotive logistics sector solutions focused on process optimization, zero-emission logistics fleets, logistics facility design and geographic placement.
Supply Chain Risk Visibility
Our partner, Everstream Analytics, uses advanced AI, risk scoring and predictions to capture, rationalize, and synthesize data from proprietary, paid, and open sources. Together, we deliver insights and other supply chain visibility systems for the automotive logistics sector to help mitigate risk and build faster, smarter, leaner, and more sustainable supply chains.
Fleet Management
DHL is the leading authority on maximizing the value and lifecycle of automotive logistics and transportation assets through best practice fleet management, improved efficiency, cost reduction and compliance with government regulations.
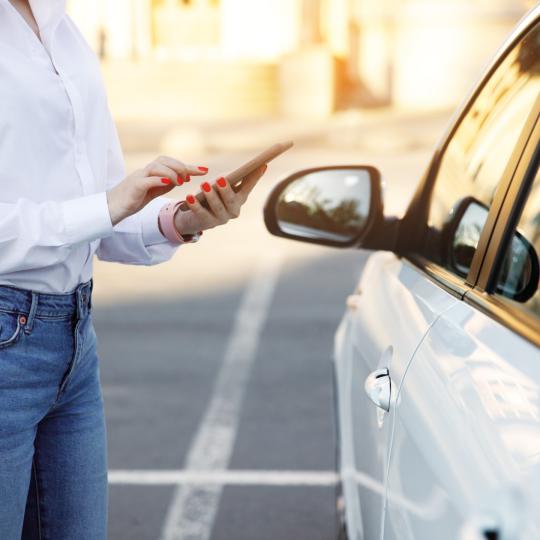
Sustainability
Our specialists deliver innovative and sustainability-motivated automotive logistics sector solutions focused on process optimization, zero-emission logistics fleets, logistics facility design and geographic placement.
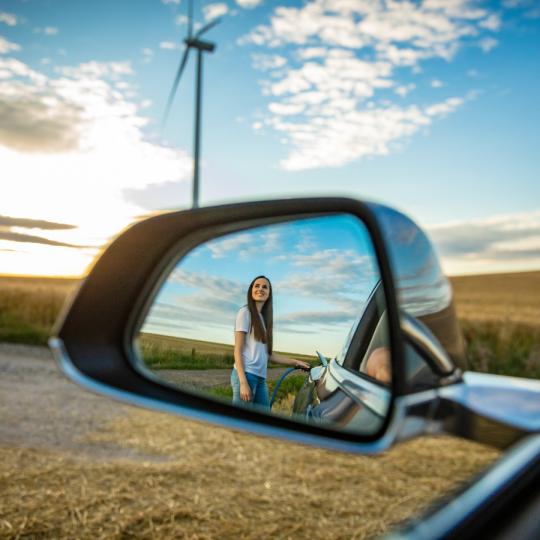
Supply Chain Risk Visibility
Our partner, Everstream Analytics, uses advanced AI, risk scoring and predictions to capture, rationalize, and synthesize data from proprietary, paid, and open sources. Together, we deliver insights and other supply chain visibility systems for the automotive logistics sector to help mitigate risk and build faster, smarter, leaner, and more sustainable supply chains.
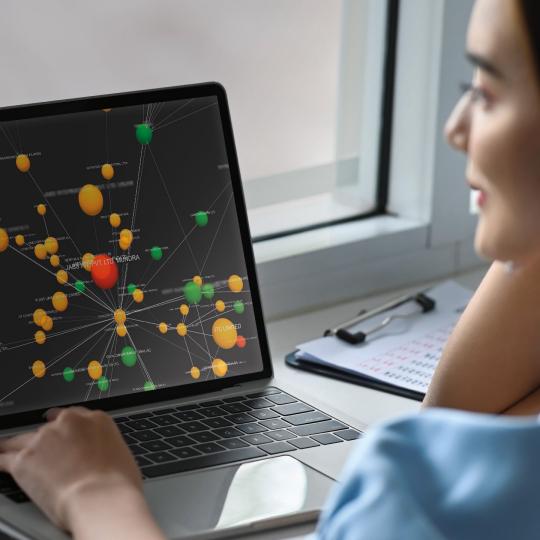
Our Commitment to Our Customers
Relentless in our pursuit of better mobility, we never stop connecting you with the world and sharing our unparalleled global reach. Innovating for a better future, we add to your competitive edge. Pioneering to take the lead in logistics, we keep you ahead of the curve. And powering the industry forward, we accelerate your business growth.
Discover More Auto-Mobility Insights from DHL
Auto-Mobility business insights and logistics innovations from across the world of DHL. Explore Our Insights and Specialized Industry Capabilities.
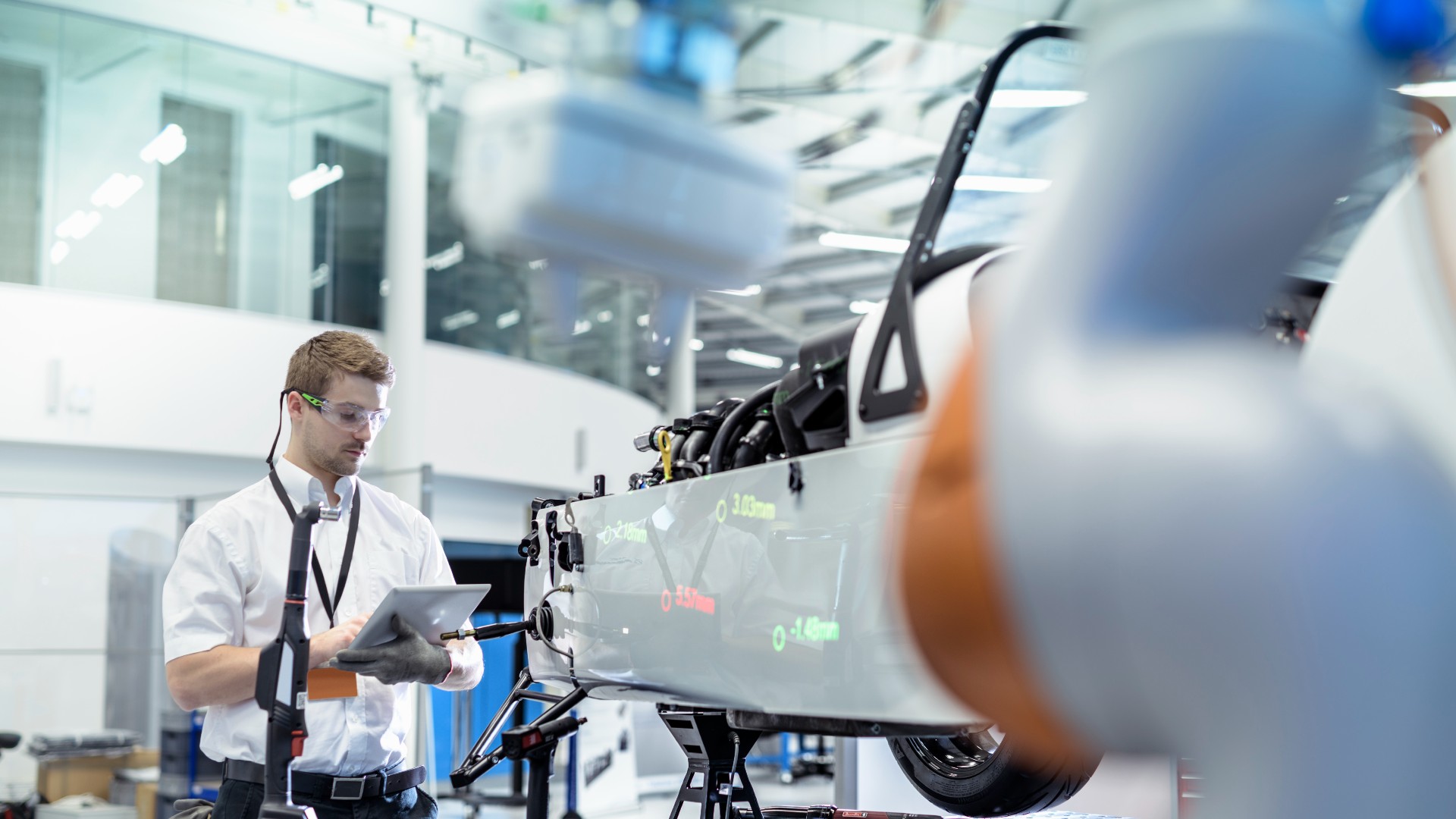
Our Auto-Mobility Experts
The Auto-Mobility experts in our divisions are:
Explore Solutions for Your Small or Medium-Sized Business
No matter if your business is growing, you are looking to expand internationally or you are simply searching for a reliable and convenient shipping services. We can help you with world-class shipping and logistics.