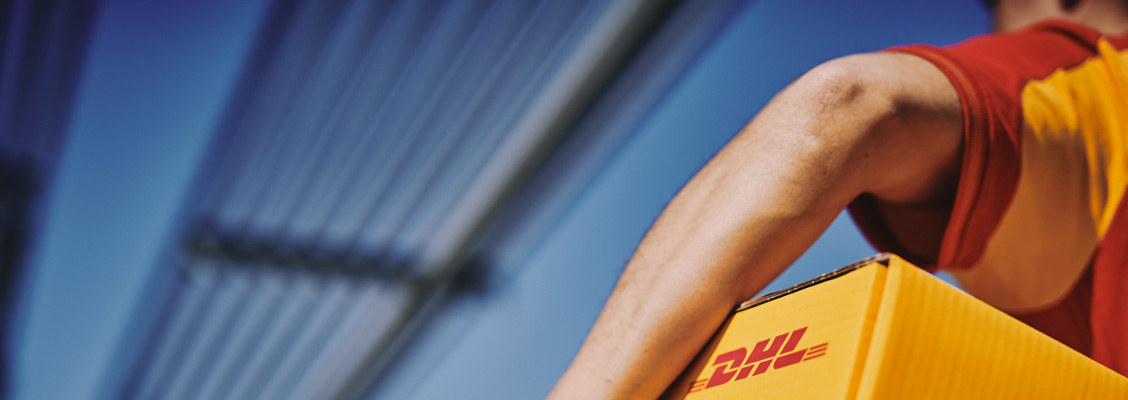
The healthcare sector relies heavily on temperature-controlled logistics to transport pharmaceutical products, bio-products, and equipment. Ineffective cold logistics measures will cost time and resources. DHL Express unpacks its cold chain transport system and outlines how it can help healthcare companies excel in this area.
Cold chain logistics describes the temperature-controlled transport of goods along the supply chain. These goods often include pharmaceuticals, equipment, and temperature sensitive foods. Cold chain logistics doesn’t only commence when the product is loaded onto the vehicle; it involves every step of the transportation journey, from initial handling to last-step delivery.
The healthcare industry relies heavily on cold chain logistics for the distribution of bio-pharmaceutical goods across borders, states, and cities. These goods, as well as specialty equipment, can be life saving. Without effective cold storage transportation, the goods can become unusable. This has real financial consequences for healthcare companies, as well as compromising a provider's ability to care for their patients.
The cold chain logistics transportation process
Many pharmaceutical companies develop products which require temperature-controlled storage and distribution. Each product comes with a temperature range that must be followed throughout the journey. The two broad categories of temperature control transportation are frozen (-15°C or below) and chilled (2°C to +8°C). Some products will require more specific environments for transport. If these environmental conditions are not met, the efficacy of the product may be diminished.
This is increasingly relevant as companies direct their research towards therapies that are derived from human cells. As these enter the market, it is inevitable that the demand for cold chain pharmaceutical logistics will increase.
To account for this demand, and as a part of the logistics 4.0 movement, transport providers have innovated technologies to facilitate reliable, temperature-controlled transport of pharmaceutical products. Products shipped by sea often employ refrigerated (reefer) containers that maintain a certain temperature through chilled airflow. When shipping pharmaceuticals by air, cool containers are the technology of choice. These containers come in passive and active formats. The passive version prevents temperature fluctuations through insulation, gel packs, ice, or liquid nitrogen. The active version uses monitors and sensors that automatically control the temperature.